Jaw crusher machines are among the most important equipment of the mining and construction industry. Designed to crush large-sized rock and mineral blocks, these robust machines reduce the material to the desired dimensions with strong pressure between the jaws. This process saves both time and energy, contributing to the reduction of total operating costs. Moreover, jaw crushers are not only limited to crushing, but also have the ability to respond to all kinds of project needs with models of various sizes and performance characteristics.
Jaw crusher selection is crucial, and the characteristics of the area where it will be used and the type of material to be crushed play a significant role. For instance, a jaw rock crusher intended for use in a granite quarry and another for crushing pebbles from a river bed will have different features. Factors such as crusher capacity, engine power, weight, and ease of use are decisive in selecting the optimal jaw crusher. Moreover, when choosing the features of the preferred jaw rock crusher model, occupational safety and working efficiency should also be prioritized.
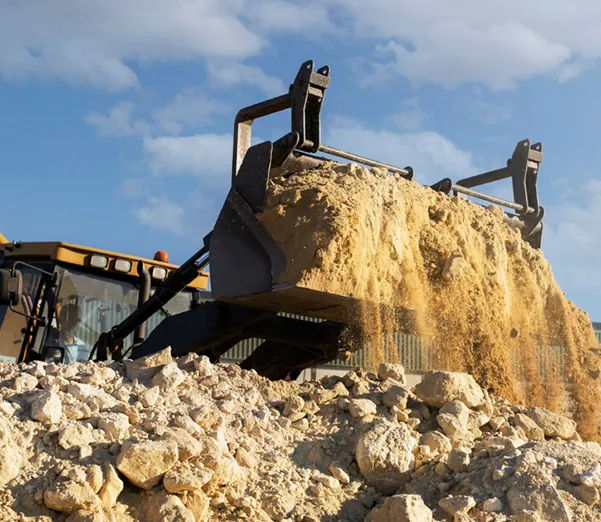
Jaw Crusher For Sale
Jaw rock crusher machines are an important component of crushing and screening plants. The prices of these machines may vary according to the technological features and capacity of the machine.
A mobile jaw crusher is a versatile option that offers the advantage of mobility. Ideal for contractors and operations that require frequent relocations, these crushers can be easily moved between sites. They provide the flexibility to crush material directly on site, which can significantly reduce material transportation costs.
For those who need an even more portable solution, a portable jaw crusher offers additional benefits. Lightweight and equipped with wheels or tracks, these crushers are easy to transport and set up. Portable jaw crushers are perfect for smaller sites and short-term projects where space and durability are considerations.
If your operation doesn’t require large-scale crushing solutions, a small jaw crusher for sale might be the perfect fit. Suited for laboratories and small-scale operations, these crushers provide efficient crushing without occupying too much space or requiring huge investments, making them an economical choice for small businesses or startups.
For tougher materials, a jaw rock crusher is designed to take on the most challenging tasks. These crushers are built to handle large, hard, and abrasive materials, like granite or recycled concrete efficiently. The robust design and powerful mechanics ensure that even the toughest rocks are broken down.
Jaw rock crusher for sale can be found in various capacities and sizes. These specialized crushers offer enhanced durability and performance in breaking down large rocks into manageable pieces for further processing or use in construction.
You can contact CONMACH for detailed information about the machines.